Blog list
CNC lathe tool setting method
- 10 / 30 / 2024
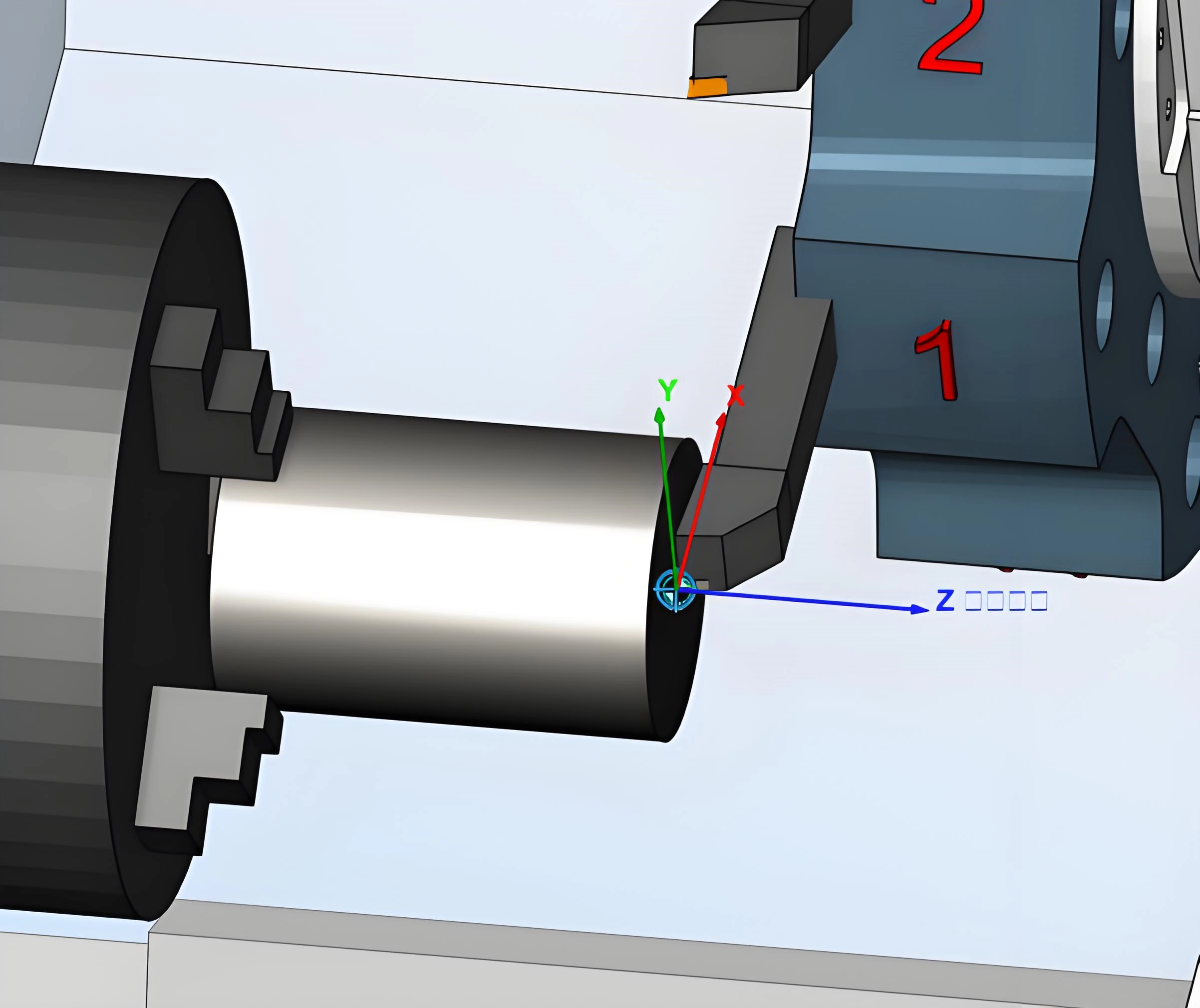
1. Trial cutting method
The trial cutting method is a tool setting method widely used on CNC lathes. It has higher precision, lower system requirements for CNC lathes, and lower performance requirements for the equipment itself, so it has been well used in the field of mechanical processing. CNC lathe test cutting method tool setting is accomplished by using the CNC lathe's detection device to detect the coordinate position of the processed part or tool in real time. Taking the absolute trial cutting method as an example, the specific operation method is: clear the CNC lathe system through the corresponding program instructions, then place the workpiece on the chuck of the CNC machine tool, start the machine tool, and quickly set the reference tool to move to the processed part. Nearby, use the reference tool to cut the outer surface of the workpiece, record the X coordinate value on the CRT at this time, keep the axial size unchanged, retract the tool longitudinally, measure the size and diameter of the workpiece, and input this value into the CNC system for tool compensation At the corresponding position of the column, the system will automatically calculate the offset of the tool and record the X coordinate point as the key point coordinate system of the workpiece. Use the same method to cut the end face once, keeping the longitudinal dimensions unchanged, and record the Z coordinate value on the CRT. At this time, you can enter the offset amount in the Z direction in the tool compensation column. Normally, this value is entered as 0. Simplify complex coordinate values in programming operations. However, the input value can also be determined by comprehensively considering the influence of the workpiece coordinate position. At this time, the CNC system records the coordinate point as the zero point in the Z-axis direction of the workpiece coordinate system. Through the above operations, the tool setting operation can be completed, and then the next step can be started.
2. Tool setter
Generally speaking, tool setters are divided into in-machine tool setters and external tool setters. Typically, in-machine tool setters are used on CNC lathes. On a CNC lathe, the tool is usually mounted directly on the tool holder. Or install it on the tool holder through a fixture, then install the workpiece on the chuck, use a tool setter to set the tool, and combine it with the CNC lathe system to complete the establishment of the workpiece coordinate system. This tool setting method replaces the traditional manual tool setting method and can significantly improve the tool setting accuracy. The description of this knife setting method has been recorded in relevant literature and will not be repeated here. The tool setting method using a tool setter is currently the most accurate tool setting method. However, this method of setting up the tool requires purchasing an auxiliary device with a tool setter. The investment is high and the loading and unloading tools are laborious. However, it can significantly save tool setting time.
CatekCNC machine automatic tool setter
RELATED MODELS
We recommend some related models for you...
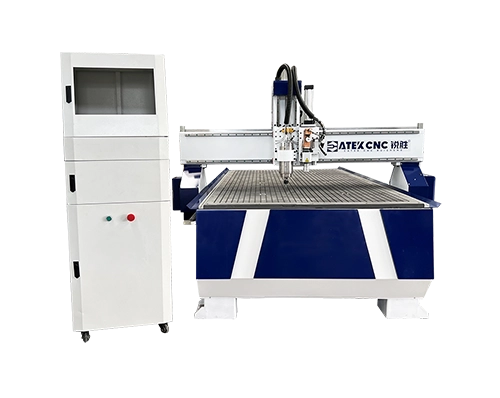
The CNC Router With Vibration Knife adds a vibration knife to the ordinary 1325, which enables it to carve hard materials while increasing the ability to cut flexible materials, making it more widely used.
$3,800.00~$4,500.00
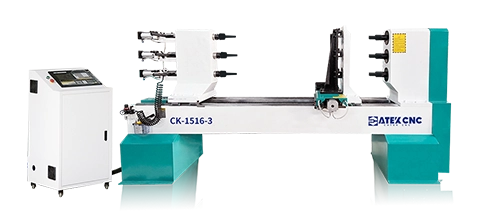
The three-axis six-knife CNC wood lathe is a three-axis six-knife design that can process three pieces of wood at a time. Six knives are fed in at the same time, which can greatly improve production efficiency and is suitable for batch processing of the same products.
$4,750.00~$5,880.00
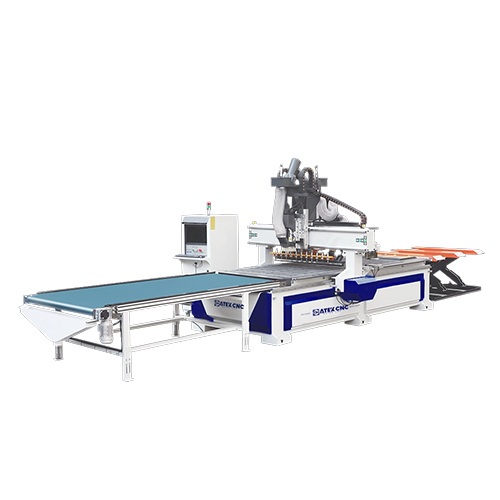
Automatic loading and unloading ATC CNC Router has automatic tool changing function, and also adds full-automatic loading and unloading function, which saves loading and unloading time, greatly improves processing efficiency and saves labor costs.